Detailed Discussion on the Design and Research of Intelligent Valve Core Assembly System
Introduction
Since the assembly system is a production line and an intelligent manufacturing unit, with the continuous improvement of intelligent control technology and refined processing, its degree of automation continues to increase. Finish. The valve core control intelligent assembly system designed in this paper realizes the core automation of material selection and valve locking, and the defective products are integrated with the detection system to sort the assembly. Adopt PLC and human-machine interface to carry out the system, and the mechanical structure is designed and reasonable. The completion of the design of this system greatly improves the production efficiency of the valve core mounted on the valve, and provides an example for the construction of this type of system.
With the rapid increase in the number of valve parts, the air volume continues to increase, which is the degree to which the automatic driving car is on the door, and the core of the car on the door is more and more frequent, and the door cannot be locked. One can realize the intelligent detection function The intelligent module can realize the intelligent problem on the intelligent module [1]. Improve production efficiency and good rate.
1. Difficulty analysis of valve core and its assembly process
In this study, after absorbing the design experience of other automatic assembly systems, the existing semi-automatic assembly system was analyzed, and the mechanical part of the system was completely designed based on the simulation of the valve core assembly process. In the system design plan, we strive to make the processing of the mechanical parts convenient, minimize the cost, make the assembly of parts simple and easy, and make the system have a certain degree of openness and expandability, in order to enhance the reliability and efficiency of the system. , and lay a good foundation for improving the cost performance of the system .
The valve core assembly system is mainly divided into three parts in terms of its mechanical structure design, namely: two assembly parts at the upper left corner of the workbench, three assembly parts at the lower left corner and seven assembly parts at the right side of the workbench part. The technical difficulty of the two-piece assembly lies in how to ensure the circular shape of the sealing ring. During the cutting process, it will be subjected to the axial extrusion force of the blade, so it is easy to deform . Secondly, during the assembly process, when a cored rod is detected on the transfer tooling component, it is necessary to realize the screening and assembly between different components of the door core through vibration. Therefore, each component falls in the corresponding position to become the assembly link. The process difficulty lies in . The above problems are the main reasons for the increase in the defective product rate in the valve core assembly at this stage. Based on this, this paper optimizes the process of valve core assembly, and adds a quality inspection system to improve the qualification rate of valve core assembly.
2. Intelligent system design of valve core on valve mouth
-
2.1Intelligent valve core assembly scheme design
The operation interface and the PLC form a logic control part, and the detection system and the PLC have two-way information flow to collect the status data of the assembly system and output the control signal. As the executive part, the drive system is directly controlled by the PLC output part. Except for the feeding system, which requires manual assistance, other processes in this system have realized intelligent assembly. Good human-computer interaction is achieved through the touch screen. Considering the convenience of operation in the mechanical design, the door core placement box is adjacent to the touch screen. The detection mechanism, the door core top-opening blowing component, the valve core height detection component and the blanking mechanism are respectively arranged around the turntable tooling component, realizing the assembly line production layout of the door core assembly. The detection system mainly completes core rod detection, installation height detection, quality inspection, etc., which not only realizes the automation of material selection and valve core lock, but also ensures the stability and high efficiency of the assembly process. The structure of each unit of the system is shown in the following figure.
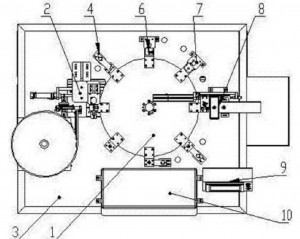
As shown in Figure 1, the turntable is the central link of the entire process flow, and the assembly of the valve core is completed by the drive of the turntable. When the second detection mechanism detects the component to be assembled, it sends a signal to the control system, and the control system coordinates the work of each process unit. First, the vibrating disc shakes the door core out and locks it in the intake valve mouth. The first detection mechanism will directly screen the valve cores that have not been successfully installed as bad materials. Component 6 detects whether the ventilation of the valve core is qualified, and component 7 detects whether the installation height of the valve core meets the standard. Only products that are qualified in the above three steps will be picked into the good product box, otherwise they will be treated as defective products.
2.2 Design of key components of valve core assembly system
As the key process of installing the valve core on the valve, locking the valve core has very high requirements on the accuracy of the movement position of the valve core, so it needs the coordination of the longitudinal and lateral mechanisms to complete. In the design of this part, it is decomposed into a single action, the discharging action of the valve core, the locking action of the locking lever and the action of loading the valve core on the valve nozzle. Its mechanical structure is shown in Figure 2.
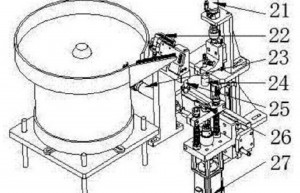
As can be seen from Figure 2, the mechanical structure of the valve core assembly is divided into three parts. The three parts work in coordination without affecting each other. When the independent action is completed, the cylinder pushes the mechanism to move to the next assembly position. In order to ensure the accuracy of the moving position, the comprehensive design of electrical control and mechanical limit is adopted to control the error within 1.4mm. The valve core and the center of the valve nozzle are coaxial, so that the servo motor can push the valve core into the valve nozzle smoothly, otherwise it will cause damage to the parts.
Stalling of the mechanical structure or abnormal pulses of electrical signals can cause slight deviations in the assembly work. As a result, after the valve core is assembled, the ventilation performance is not up to standard, and the assembly height is not qualified, which leads to the failure of the product. This factor is fully considered in the system design, air blow detection and height detection are used to sort bad products.
2.3 Design of valve core assembly control system
The control system in this design mainly includes PLC logic control, servo motor drive system, detection system and HMI man-machine interface. The servo drive system is mainly composed of a servo motor, a reducer, etc., which drives the mechanical parts to move after receiving the signal. The servo system can realize precise positioning and speed adjustment under the control of PLC. The detection system includes photoelectric sensors, light sensors, laser sensors, etc., which mainly realize the functions of positioning detection, parts detection and identification, and process sequence matching. HIM man-machine interface adopts graphical programming module, which can realize good man-machine interaction. The operator can directly control the system through the operation interface, and the assembly process and parameters can also be displayed directly through the interface.
The system can select manual assembly mode and automatic assembly mode through the operation interface. In the automatic mode, the system automatically assembles according to the assembly process. In the manual operation mode, the system runs in a single step, and each operation action will not run continuously. The execution of the system program starts from the sub-network of the turntable rotation, the PLC outputs the control signal control, and the servo motor drives the loading and rotation of the disk. When the turntable carries the valve core to the corresponding technological process position, the technological process subroutine runs, and the execution component executes the corresponding action according to the control signal.
3. Ending
The process flow of valve core installation on the valve is not complicated, but the requirements for the refinement of the process are relatively high. Therefore, manual assembly and semi-automatic assembly are mainly used in industrial production, and their performance and quality are unstable. In this paper, an intelligent assembly system for valve core mounted on the valve is designed, which realizes the automation of material selection and valve core locking, and detects the ventilation performance and installation height of the valve core assembly through the detection system, and the detection results are automatically Upload it to the control system to realize automatic sorting of defective products. The working efficiency and product stability of the valve core mounted on the valve nozzle are improved.
Write your message here and send it to us